Airbus is postponing its very ambitious plans to launch a hydrogen-powered turboprop aircraft with around 100 seats by 2035 by five to ten years. No specific timeline was given.
The global aviation industry has set itself the goal of achieving climate neutrality by 2050. While Boeing has not yet published any plans for hydrogen-powered aircraft, Airbus has planned to develop and launch a 100-seater turboprop aircraft by 2035. Fuel cells are to be used to generate electricity from hydrogen, which would be powered by electric motors.
Airbus has postponed this extremely challenging goal by 5 - 10 years - without specifying a concrete timeline. The reasons given are manifold and range from as yet unresolved technical challenges to the lack of green hydrogen available on the market and the fact that customers are not yet sufficiently willing to pay significantly higher ticket prices.
"Forecasts are difficult, especially when they concern the future" - according to Mark Twain, but such unrealistic plans often result from anticipatory obedience to (sometimes) excessive political goals in this regard.
If you look at the current forecasts for the production costs of hydrogen (see chart below, taken from Bloomberg), it is clear that there is still a great deal of optimism.
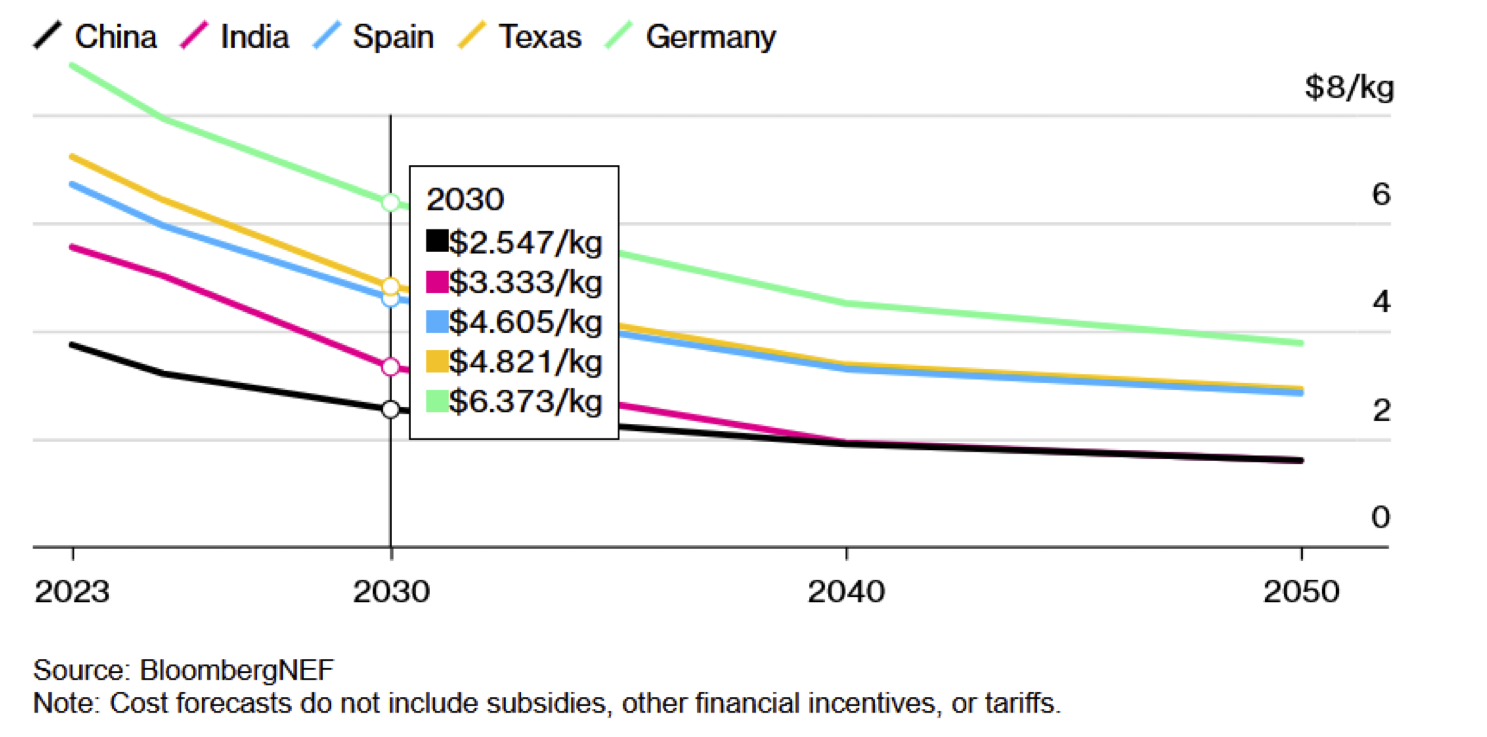
This could be due to the fact that the analyses carried out so far have not taken into account the necessary, wide system limits on the one hand, and on the other hand - due to a lack of experience - the steepness of the learning curve has been overestimated. Although a steep learning curve can be assumed for electrolysis [stacks and balancing of plant (BoP)], these are ultimately individual components that are installed in a large industrial plant. Industrial plant construction is complex per se due to the multiple interfaces, but in large-volume hydrogen production plants there has been a lack of legal requirements, standards, certification bodies and - last but not least - experience - especially as the individual components have to be purchased worldwide and transported to the construction site.
The cost trend forecast in the graph leads to production costs of around €50/MWh in China and around €100/MWh in Germany in 2050. The transport costs and hydrogen storage costs must be added to this. The hydrogen storage costs alone amount to approx. 25 €/MWh for pore storage systems (very optimistic estimate) and > 105 €/MWh for cavern storage systems. This means that with a number of cycles of one and by allocating these hydrogen storage costs to the total amount of hydrogen sold (assumption: 1/3 of the annual sales are stored), at least a further 8 €/MWh must be added for pore storage systems and approx. 20 €/MWh for cavern storage systems (number of cycles of cavern storage systems approx. 5). This is with a hydrogen purity of approx. 98%. As fuel cells require a higher purity, additional purification costs must be taken into account.
So far, the transport challenges in rededicated natural gas networks - including the resulting costs - have been considered without compressor stations. If you consider that transporting the same amount of energy requires 3-4 times the compressor capacity compared to natural gas transport, then it is also clear that the compression costs - both capital costs (very large and therefore expensive piston compressors have been used for hydrogen transport to date) and operating costs - will be high, especially as the power supply to the compressor stations must first be ensured by means of electrical lines.